Vertical Direct Chill (VDC) Billet Casting
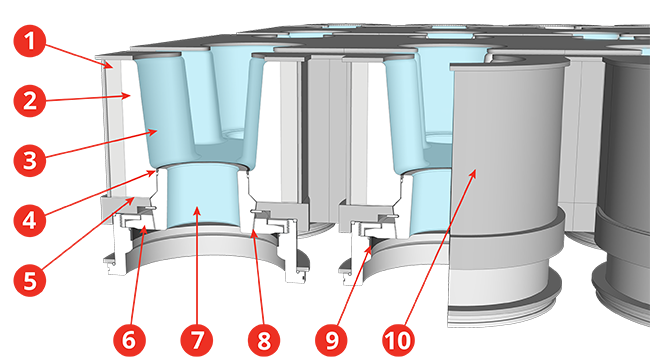
Key
The VDC billet casting process is the method most used today for production of commercial aluminium billets that will be further fabricated by either extrusion or forging. This process produces fine-grained billets with a minimum amount of segregation and at high production rates. Metal quality and minimal downtime are key to producing high-value product and scrap reduction.
Pyrotek offers proven solutions for VDC billet casting, including billet table refractory, coatings, transition plates, machined graphite, thimbles, thermocouples, refractory shapes, seals and gaskets, backup insulation and casting lubricants.
Benefits include:
- Increased metal quality
- Reduced energy costs
- Improved process efficiency
- Reduced downtime
- Customized solutions
Related Products
- Pourable Insulation
- Pyrotek Ring-Fit Transition Plates
- Original Equipment Replacement (OER) Transition Plates
Bulk Ceramic Fibers
High Temperature Fabrics
Refractory Shapes
Safety Coatings
Thermal Insulation
Additional Information
1651 Vertical Direct Chill Billet Casting Brochure EN | Brochure | English |
- Product Lines Continued – Tabletop refractory, thimbles, and transition plates
- Billet Casting Process – Casting technology insight, describe concerns of Pyrotek customers in this product area, and share some forecasting about where the market is heading
- Mastics, Pourable Insulation, Lubricants - For Billet Casting Applications