Jet Bed Dryers
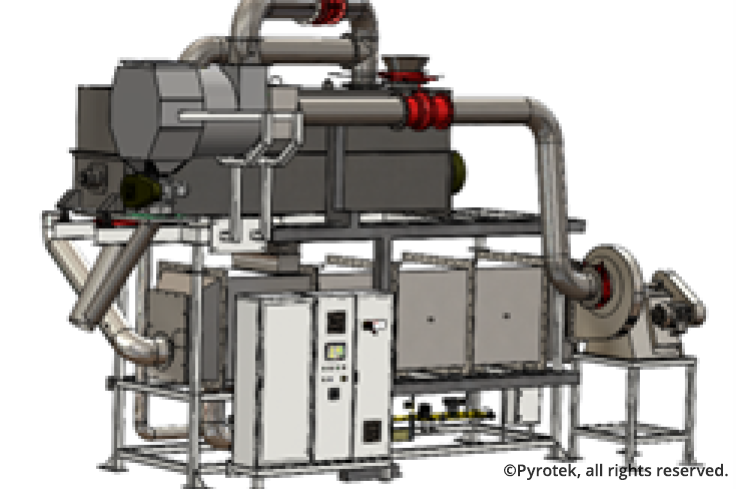
Overview
The Pyrotek Integrated Melting System (IMS) consists of equipment specifically engineered to process machining chips, converting the chips efficiently back to usable metal. The IMS system provides significant increases in recovery rates.
Pyrotek Offerings
In the aluminium industry it is understood that 1 percent burn-off of contaminent in an aluminium bath results in 1 percent melt loss. A 1-to-1 ratio. This is referred to as "contaminant induced melt loss." Testing at a Pyrotek research and development facility in Aurora, Ohio, has proven this ratio is common, and in some cases contaminant induced melt loss was shown to be as much as 2-4 percent per 1 percent of contamination. Significant cost savings can be achieved by making operational improvements. Pyrotek's IMS technology is an engineered solution to provide improvements in this area and provide high value compared with competitor technologies.
Pyrotek Jet Dryer
A compact, stand-alone pre-wired chip dryer with integrated thermal oxidiser is engineered to allow customers to position the unit so it feeds directly into a Pyrotek LOTUSS system (optional) for optimal energy and melt recovery targeted for in-house chips processing.
Chips are fed into the dryer where they are conveyed over hot air jets. The chips are dried to less than 0.3 percent moisture (target level of 0.1 percent) for best recovery in the LOTUSS vortex.
The exhaust air from the drying process is drawn into the thermal oxidiser where it is heated to 1400°F to remove the smoke. This air is then cooled down as it passes across the heat exchanger to atmosphere.
Simultaneously, fresh air is sent across the other side of the heat exchanger where it is heated up to 600-800°F, then blown into the chips in the upper deck, providing the optimum air temperature for contaminant removal.
Explosion & Fire Suppression System
Pyrotek understands that some production environments are high risk. That is why Pyrotek integrated a state-of-the-art explosion and fire suppression system into the technology designs. Pyrotek recognizes the critical importance of protecting process system equipment in hazardous environments, particularly against dust explosion hazards.
Explosion
The High-Rate Discharge (HRD) Explosion Suppression System is designed to provide an active method to protect process system equipment from a dust explosion hazard. The principle of operation for the HRD system is detection of the pressure rise during the initial stage of an explosion, followed by fast injection and homogeneous distribution of an extinguishing agent into the protected vessel. The chemical suppression system consists of a controller, pressure or optical detectors, and the high-rate discharge HRD bottles.
If a deflagration develops, the pressure inside the vessel will begin to build rapidly. The explosion pressure detector will detect the rate of pressure rise over a certain time period and activate the HRD bottles. Once activated, the HRD bottles will disperse suppressant into the protected vessel, inhibiting the explosion from further developing, thus reducing the pressure and preventing any vessel breach.
Fire
The argon fire suppression system is designed to extinguish fires effectively. It stores argon as pressurized gas in multiple cylinders connected through a common discharge manifold. When triggered by explosion-proof thermal detectors, the system releases argon to reduce the residual oxygen concentration to a level where combustion is no longer sustainable, effectively putting out the fire.
Integration
The integration of these components, along with a focus on safety and the reduction of contaminants, makes Pyrotek's technology a valuable solution for companies in the aluminium industry. By addressing issues related to melt loss, drying efficiency, and safety, Pyrotek's technology can help companies improve their operational performance and reduce costs, ultimately providing a competitive advantage.
Pyrotek.com Blog | Pyrotek Installs Another Integrated Melting System (IMS) at Customer Site
- Reduced contaminant-induced melt loss, improving overall aluminium recovery and minimizing material waste
- Customized solutions: Pyrotek offers tailored solutions that can be adapted to specific client needs and processes, increasing flexibility and efficiency
- Energy efficiency: the technology optimizes energy usage, reducing operational costs and minimizing environmental impact
- Enhanced process control: integration of Pyrotek technology allows for better control and management of aluminium processing, resulting in consistent and reliable outcomes
- Pyrotek’s commitment to safety - integration of explosion and fire suppression systems that provide critical protection against dust explosions and fires, safeguarding lives and equipment
- Jet Bed Dryers
1301 Jet Bed Dryer EN | Datasheet | English |