Skim Dams
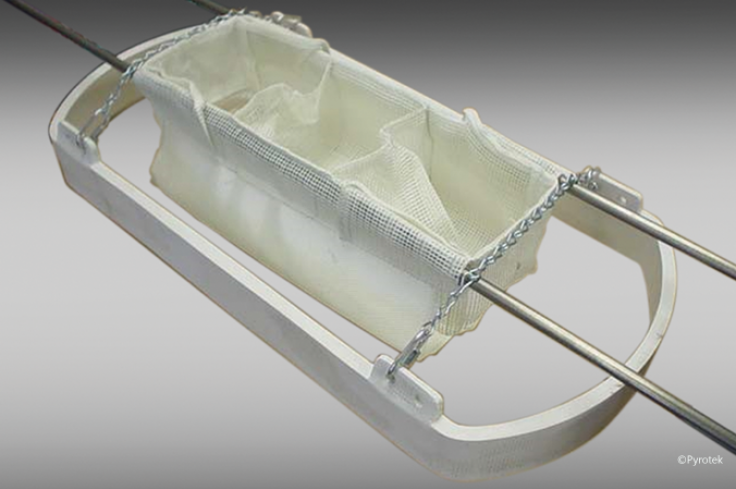
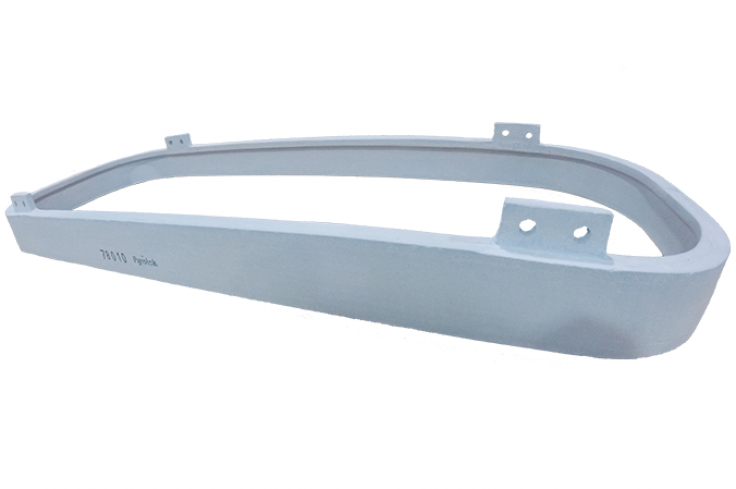
Overview
A skim dam is designed to float on the metal surface and prevent oxides introduced near the downspout from moving across the top of the molten metal in an ingot mould and rolling down the outside of the ingot. These oxides can cause severe cracking in solidified ingots and impact total ingot recovery for the plant. One study of a 17,000 tonne campaign of AA-5182 saw total ingot recovery improve from 96.6% to 99% from introduction of a skim dam. Skim dams are particularly recommended for use with 5XXX alloys due to the tendency of these alloys to generate more oxide or skin.
Pyrotek Offerings
There are many design features that impact the effectiveness of a skim dam. The Pyrotek sales team can help determine the optimal size, hanger style, and positioning to increase the likelihood of trapping oxides. Combined with expertise and innovation in thermally-formed (TF) combo bag technology, Pyrotek offers a complete, application specific package for delivering clean metal to the mould walls.
Proper material selection can also make a difference. For example, skim dams made from Pyrotek's reinforced fibreglass material (RFM®) naturally sit lower in the melt than traditional calcium-silicate dams, and therefore are more prone to interaction with oxides traveling under the surface. The strength of the RFM allows for thinner designs for squeezing into tight spaces or enhanced shape optimization, while also providing up to three times longer life than CalSil dams depending on the application. They are also lightweight and easy for operators to manipulate.
Skim dams can be used in both direct chill (DC) and electromagnetic (EMC) casting processes.
- Customizable solution for oxide control at ingot head
- Measured improvements for total ingot recovery
- Visibly noticeable ingot surface quality improvements
- Longer life products
1379 RFM Skim Dam EN | Datasheet | English |
676 RFM CS FS SiC ZR EN | Datasheet | English |
1127 Refractory Board Products EN | Datasheet | English |
1716 Vertical Direct Chill Slab Casting Brochure EN | Brochure | English |